A Data-Driven Approach to Supply Chain Optimizations
Achieving continuous supply chain optimizations through aggregated data analysis
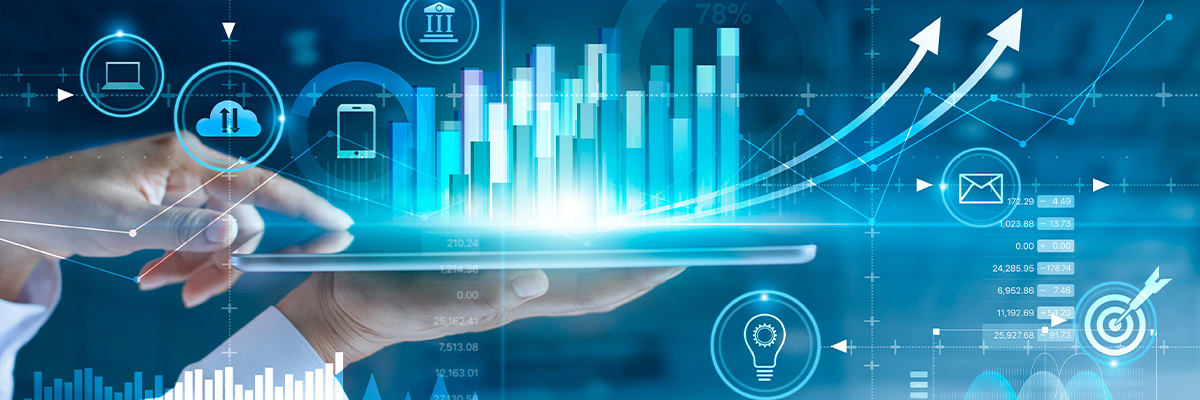
With the fast-paced nature of the supply chain, it can be challenging to protect products for food, pharmaceuticals, and other industries from points of origin to final destinations due to a lack of visibility into where the cargo is, and what is its condition at any given moment. Without clear, real-time insights, it can be difficult to make supply chain optimizations that maintain product integrity, meet compliance mandates, control costs, and manage risks.
Thanks to the use of cargo monitoring sensors based on the Internet of Things (IoT) technology, companies can now track cargo right down to the item level. When sensors travel with the cargo, there is greater granularity into real-time temperature and location data captured than when sensors only track drivers, shipping containers or trailers.
With effective supply chain data analysis, companies can rest assured that their cargo is in good condition at any given moment.
Strategies for Effective Supply Chain Optimizations
Sensitech has found that customers who use a multi-pronged approach to collect, manage, and analyze their supply chain data have a better opportunity to make effective supply chain optimizations. With this approach, customers can effectively use data for:
- Transactional decisions. Collecting real-time and historical data helps customers make day-to-day tactical decisions such as acting on alerts to intervene on in-transit shipments, or using that data to facilitate dock-level accept or reject decisions by shipment on arrival.
- Continuous improvement decisions. Aggregating data over time develops in-depth supply chain data analyses to help customers identify trends and patterns, facilitate efficiencies in quality control and operations, and create long-term continuous improvements.
This approach is backed by these three key data strategies:
- Collect clean and comprehensive data that drives actionable outcomes and leads to measurable improvements.
- Consume data in a way that facilitates both tactical and strategic decision-making.
- Analyze the data and collaborate with supply chain partners to improve quality, reduce costs, and increase efficiency.
Quality, logistics, operations, and purchasing personnel are often responsible for managing complex global supply chains, including the data strategies mentioned above; however, companies like Sensitech can help them develop an effective data-driven program for monitoring and improving cold chain logistics that goes beyond just product quality.
Sensitech programs include well-developed processes for collecting, consuming, and using the data; innovative software for managing and analyzing the data; and expert personnel that can address supply chain optimizations while helping customers gain operational efficiencies.
Supply Chain Optimizations Start With Effective Data Collection
This section examines the first strategy, which focuses on the importance of collecting clean and comprehensive data to drive measurable improvements, and the second strategy, utilizing data to facilitate smart decision making. Here are a few examples of how our customers utilize these strategies today.
Data must be comprehensive yet not extraneous
Your supply chain data analysis is only as good as the data you collect. Poor quality data can actually lead to bad decisions, which can be costly. That’s why we help our customers ensure they are collecting the right data at the right time.
For instance, we’ve helped many customers who monitor temperature-sensitive products transition from manual devices to hands-free devices equipped with radio frequency and real-time capabilities so they can be more proactive and save labor costs. For better analytics, these customers are augmenting time, temperature, and location data with other complementary data from telematics as well as shipment information from ERP, transportation, and logistics systems and product quality information. Thanks to these supply chain optimizations, these companies can now automate data collection and integration, which saves costs and improves data integrity.
With the help of our real-time technology and data management, customers can integrate analytics into their business processes and go from making tactical dock-level decisions to more strategic ones that can have a direct and indirect impact on improved quality and operations.
Comprehensive farm-to-fork visibility
A major fast-casual restaurant chain was an early adopter of hands-free, real-time temperature and location monitoring sensors and soon took full advantage of what Internet of Things (IoT) technology had to offer.
With IoT-based sensors, the restaurant chain eliminated the need to manually retrieve and download data. Temperature, light, and location data give the company significant visibility into its supply chain so it can react proactively to exceptions. For example, with real-time alerts, the chain can intervene immediately when temperature and transportation issues occur. It also has a better understanding of route performance, and most importantly, it has been able to reduce rejected loads and product loss.
The IoT devices travel with the product, rather than the driver, trailer, or unit, which allows for real-time monitoring of the entire chain, from suppliers and distribution centers all the way to the restaurants. With comprehensive end-to-end visibility and automated segmented supply chain data analysis, it is easier for the company to pinpoint where cold chain and logistics breaks are occurring, which is helping the company decrease labor costs, improve response time, and reduce product loss.
Figure 1: Real-time alerts from IoT sensors allow this customer to intervene immediately when temperature excursions occur.
On-site cold chain evaluation
Sensitech performs regular reviews of customer data and makes recommendations on how to optimize our customers’ supply chain visibility programs. In this example, we used analytics to help identify a problem within the shipping segment of this customer’s cold chain.
This fast-casual restaurant chain was experiencing higher-than-desired temperatures on some of the routes where frozen french-fried potatoes were shipped via rail cars. Sensitech performed an on-site cold chain evaluation, where we used monitors to collect product and ambient temperature data during the entire shipment of the products. We also observed the shipping process and used time and temperature data to determine that the carbon dioxide (CO2) used to cool the product while in transit was dissipating before it arrived at the shipping destination.
The customer decided to no longer use CO2 rail cars, and with this process change, the temperatures for these shipments improved dramatically.
Figure 2: An on-site analysis and review of data helped identify the source of this customer’s temperature excursions.
Large-scale supply chain data analysis made easy
A major U.S. food distributor has incorporated data into its decision-making process in almost every aspect of its supply chain. The customer takes advantage of Sensitech’s visibility platform to help food safety, transportation, and product managers make decisions regarding daily tasks for inbound, outbound, storage, and shuttle yard operations.
These managers can document and execute corrective actions for exceptions with data that is reported and consumed in real-time and accessed through a dashboard. They also have access to analytics that help identify trends and pinpoint the causes of exceptions for quicker decision-making.
From the dashboard, the managers have access to all the tools they need to manage everyday business and optimize food supply chains while corporate and regional managers gain extensive data visibility for executive-level strategic reviews.
Figure 3: The analysis of temperature alerts helped this company take corrective actions and reduce excursions over time.
Using real-time data to filter product quality in inbound shipments
Sensitech helped a top U.K. supermarket chain transition from conventional to real-time monitoring devices for inbound shipments from various suppliers to its distribution centers. The goal was to use real-time data to achieve greater efficiency and improved quality in the receiving process.
The supermarket chain also completed a system integration where product information and logistics details from its ERP system were automatically connected to the tracking devices. This allowed them to collect a more robust data set to drive even more supply chain optimizations.
Sensitech also helped this customer develop and implement a traffic light alerting system that could be used as triage methodology to assess temperature-abused product and address in-transit delays. The alerting system categorizes shipments based on the severity of temperature abuse and delays during transit. For instance, a green light indicates product that is 100% acceptable, while amber means the product is of questionable quality, and red means the product has experienced a temperature excursion or incident that renders it unacceptable.
Figure 4: This customer uses a traffic alert system that helps triage accept and reject decisions.
The ability to triage inbound shipments in this way significantly improved the efficiency of the receiving process and ultimately, the ability to make better dock-level decisions.
Engaging Stakeholders with Supply Chain Data Analysis
This section looks at how the use of comprehensive data can help organizations drive supply chain optimizations through the more effective engagement of partner stakeholders such as suppliers, carriers and receivers.
This can be achieved in many ways, including sharing quality assurance (QA) standards, sharing responsibilities when exceptions occur, and looking at historical data across the supply chain to identify opportunities for continuous improvement. Here are a few examples:
Improved vendor accountability.
This Sensitech customer is a producer of organic chicken, and the company utilizes real-time devices to monitor in-transit temperatures and manage delivery logistics.
Sensitech helped the producer develop a “Carrier Score Card Report” that grades carrier performance based on a combination of how well ambient temperature is maintained during transit and the consistency of on-time arrival rates. Armed with this information, the customer can make tactical decisions based on temperature and delay alerts and strategic decisions about carrier partnerships. As a result, the company has improved the fulfillment of its KPIs significantly.
Better quality through shared data
An international fast food chain shares its U.S. national quality and compliance data from Sensitech reports with its suppliers and distribution centers on a weekly, monthly and quarterly basis to manage compliance and quality. The customer also gives out annual awards to encourage its supply chain partners to make operational changes to improve performance.
By sharing this data, the customer has been able to reduce the percentage of non-compliant shipments from 6.4% to 0.5% in just three years. This fast food chain has been diligent in taking action to train suppliers and receiving distribution centers on best practices. The company also conducts frequent supplier visits and other continuous improvement activities.
The company is also in the process of merging the quality and compliance data with complaints from its restaurants to make the corrective action process more efficient.
Figure 1: This customer shares reports like this with third-party vendors to improve performance.
Improved route management
Sensitech helped an international burger chain incorporate cold chain monitoring into its supply chain management protocol and share responsibilities with its partners to manage quality and logistics.
The suppliers were given the task of acknowledging and addressing real-time temperature alarms. All stakeholders, which included suppliers, receivers, and logistics managers, had the responsibility of tracking shipments to address transit delays and any necessary rerouting of shipments. The company’s logistics team was then able to use a Sensitech tracking system to uncover how it should re-route trucks during a hurricane that impacted a majority of the U.S. East Coast.
Figure 2: Real-time and predictive data help this company choose new, safer routes for its product.
Continuous improvement through data analysis
For a produce cooperative, a long-time Sensitech customer, the evaluation of historical data helps drive continuous supply chain optimizations. Sensitech collected over twelve years of historical data and combined it with four years of more recent real-time data collected from newer IoT-based sensors. The data is aggregated and analyzed to provide long-term benefits of a cold chain monitoring program.
The historical data is used to measure non-compliant performance over time through KPIs, such as mean temperature as well as rate and percentage of shipments out of spec. For example, as seen in the graphic below, the data shows that the average mean temperature month over month and year over year continues to decrease, which translates into improvement over time.
Figure 3: This historical analysis helped this customer measure continuous improvement year over year.
The historical data is also broken down by supplier, carrier, and receiver. In one case, the data led to on-site evaluations to identify the root causes of issues. Data collected for product temperature on the wall versus off the wall helped Sensitech identify that the product was improperly loaded onto a truck and placed directly against the truck walls. The company updated its standard operating procedures (SOPs) and made operational changes that eliminated these improper practices.
Final Thoughts: Data-Driven Supply Chain Optimizations
It’s important for companies that want to improve supply chain quality to have a multi-pronged best practices approach to collect, manage, and analyze their data. As the examples show, Sensitech’s data can drive visibility, which is a strategic way to improve quality and operational efficiency.
To learn more about the technology and services behind these customer successes, Contact Us today.