How to Ship Medicine that Needs Refrigeration
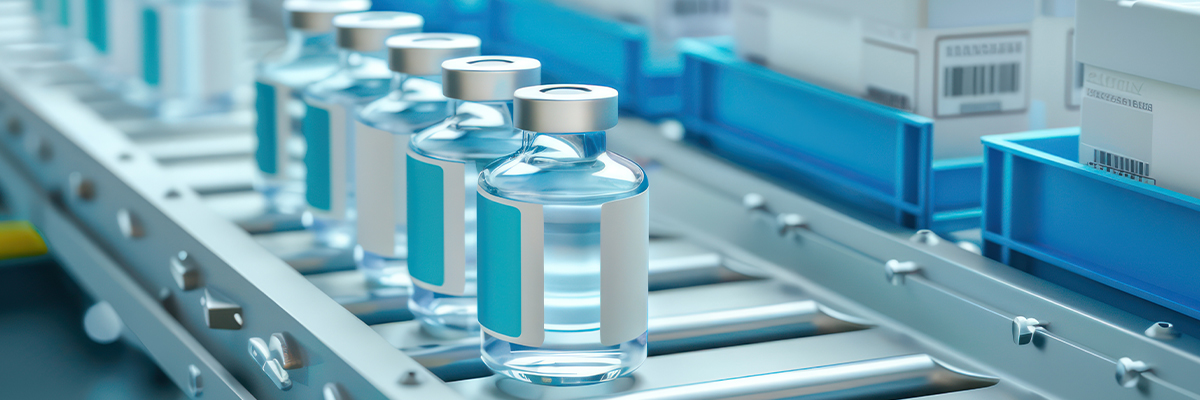
Refrigerated transportation is vital for distributing essential medicines. Many of these medications are temperature-sensitive, requiring precise temperature control during transport to preserve their effectiveness and ensure they are safe to administer to patients.
Let’s explore how refrigerated medicines are shipped, the regulations that affect the shipping process, and some best practices to maintain the integrity of the medicine cold chain.
The Medicine Cold Chain Explained
Around half of all new medicines require refrigeration during transport and storage. These medicines are sensitive to temperatures outside of their label-stated ranges, which can cause them to lose their effectiveness or even become unsafe for administration.
The medicine cold chain seeks to ensure that pharmaceutical products are maintained within their required temperature ranges from the moment they leave their manufacturer until the point of administration to patients. This process requires pharmaceutical-grade refrigeration equipment in both trucks and storage areas, packaging that can preserve cold temperatures, and precise temperature monitoring that can be documented to be highly accurate to the rigorous standards set by regulatory bodies.
The cold chain is a critical component of the pharmaceutical industry, protecting patient safety and product quality. Because of this, it is heavily regulated, and a broken cold chain can lead to ineffective medicines and significant financial losses for pharmaceutical companies.
Regulations for Refrigerated Medicine
In the United States, the United States Pharmacopeia (USP) sets standards for the storage and transportation of medicine. The two key standards are USP <659>, which specifies packaging and storage requirements, and USP <1079>, which provides guidelines for good storage and shipping practices. USP <1079.3>, made official in December 2023, defines the science of temperature and humidity monitoring. It describes available temperature monitoring technologies and provides recommendations for qualifying their performance.
While these are the two key standards in the United States, it is important to be familiar with any other regulations, guidance, and best practices that may affect the products being shipped.
Considerations When Shipping Medicine That Needs Refrigeration
When shipping refrigerated medicine, several factors must be considered to keep medications within safe parameters in the cold chain:
Temperature Range
For the entire duration of the shipping process, medicines must be kept within the temperature range at which they remain stable. The most common range is between +2°C and +8°C (+35°F to +46°F), though certain products can have significantly different temperature requirements. Any deviation above or below this range may compromise a medicine’s quality and render it unusable.
Humidity
Although a less common requirement in the pharmaceutical space, humidity may affect the stability of medications. Humidity should be controlled within the packaging environment and monitored. Dataloggers such as the TempTale GEO X real-time temperature monitoring solution can monitor humidity in addition to temperature. This is particularly necessary when shipping to more humid regions, such as the United Arab Emirates and areas of South America.
Light Exposure
Some medications, such as vaccines and insulin, are light-sensitive and require protection from light to maintain their effectiveness. A sophisticated temperature monitor such as the TempTale GEO X will provide monitoring for light exposure in addition to temperature and location.
Light incursion monitoring is also beneficial for knowing when a package or truck has been opened, providing better understanding of when a shipment has changed hands, and offering better data from which to analyze any recurring issues in a shipping lane.
Packaging
Maintaining proper temperatures during shipping requires the use of specialized packaging solutions. Specially designed insulated containers that accommodate a temperature monitor are the most common solution. These containers use cold packs to maintain proper temperatures, and companies sometimes also utilize thermal covers to ensure protection against external temperature changes.
Ideally, a packaging solution will be neither overbuilt (providing more temperature protection than a product requires on a specific lane) or underbuilt (providing minimal protection and therefore requiring faster shipping to ensure ambient temperatures cannot affect the product inside). This shipping and packout optimization ensures a cost-effective and efficient shipping process for mature companies, and helps counteract the ever-changing impacts of climate change and supply chain disruptions.
Temperature Monitoring
The ability to demonstrate that products were maintained at their correct temperatures during the entire shipping process is critical in the medicine cold chain. Continuous temperature monitoring ensures that any temperature deviations are detected and addressed, ensuring that the pharmaceutical products reaching patients are effective and safe to administer.
Temperature monitoring must be conducted using highly accurate devices designed for life sciences use, with certificates of calibration that document their accuracy. All temperature monitoring must be documented in order to demonstrate that correct temperatures were maintained during shipping.
Documentation
Proper documentation of shipping conditions is essential for compliance and traceability. It is important to use a datalogger that accurately records temperatures and produces a reliable data report that can be stored in an audit-ready system of record.
Documentation ensures there is no doubt that refrigerated medicines were shipped properly and arrived safe to administer.
Optimize Your Medicine Cold Chain With Real-Time Tracking
Real-time temperature monitoring solutions use cellular communication to provide live temperature and location data while a medicine is in transit, allowing supply chain partners to understand where a shipment is and whether proper temperatures are being maintained.
There are many benefits to real-time pharmaceutical temperature monitoring, including immediate alerts in case of temperature deviations, which can enable product-saving actions. Having a shipment’s temperature data automatically synchronized to a system of record for improved compliance rates is another benefit, as is the gathering of rich location data that allows effective supply chain optimization.
Final Thoughts
Shipping refrigerated medicine is a process that requires careful planning and execution. But with the right approach, and with the right tools, it doesn’t have to be difficult. The guidelines above demonstrate the best practices followed by pharmaceutical companies to ensure that medications remain stable throughout their journey, and safe and effective to administer to patients.
Interested in learning more about how Sensitech can deliver comprehensive cold chain visibility and regulatory guidance that scales with your business? Contact Us today.