Combatting Grocery Supply Chain Challenges: 3 Tips for Supermarkets
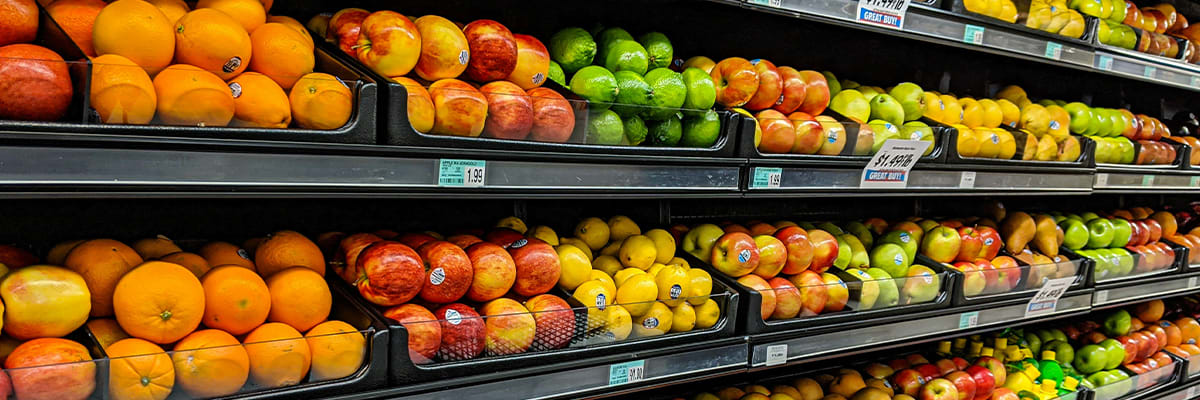
An Overview of Today’s Grocery & Supermarket Supply Chain
The supply chain that delivers fresh produce to grocery stores involves many steps and players, including farmers, distributors, transporters, wholesalers, and retailers. Here is a simplified overview of the supply chain:
1. Farming
The process of growing and harvesting produce starts at the farm, where farmers use various techniques to produce crops, such as planting, watering, and fertilizing.
2. Harvesting
Once the produce is ready, it is harvested and sorted to ensure only high-quality items are sent for distribution.
3. Packaging
After the produce is sorted, it is packaged to protect it during transit. Packaging may include boxes, crates, or containers.
4. Transport
The packaged produce is then transported from the farm to the distributor or wholesaler. This can be done by truck, rail, or air, depending on the distance and urgency of delivery.
5. Distribution
Once the produce arrives at the distributor or wholesaler, it is sorted again, and the distributor or wholesaler will sell it to retailers, such as grocery stores.
6. Retail
The grocery store then receives the produce and displays it for sale to customers.
Many potential issues can arise throughout the supply chain, such as damage during transit, delays in delivery, or quality issues. These challenges can be particularly acute for products such as fresh produce and flowers, which require careful handling and storage to maintain freshness and quality. Since 93% of grocers noted that they’ve seen an increase in the demand for fresh food, it’s important for retailers to develop a system that preserves quality and prolongs shelf life.
In recent years, grocery store supply chains have undergone rapid transformation in the aftermath of the COVID-19 pandemic. Shifts in consumer behavior were one source of pressure. Panic buying of essentials caused unexpected surges of demand that retailers struggled to keep up with. At the same time, staffing difficulties caused businesses from food processing plants to shipping companies to shut down temporarily or operate at reduced capacity.
However, the pandemic isn’t the only trend driving change in grocery store supply chains. The shift toward healthier eating habits and the growing demand for fresh and local produce has led retailers to focus on improving the quality and availability of fresh foods. Retailers are experimenting with different formats such as meal kits, in-store dining experiences, and more locally sourced products. As a result, they are also investing in technology to ensure better supply chain management and product tracking.
What Is Causing Supply Chain Issues at Grocery Stores?
Despite grocery stores’ best efforts, the fresh produce supply chain is far from seamless. A number of factors can lead to out-of-stock items, delayed shipments, higher prices and other pain points for consumers.
A Post-Pandemic Shift
Safely delivering fresh, healthy produce to supermarket shelves is a complex process with multiple stakeholders involved. Growers harvest, sort and package their products, which are then shipped by truck, air or rail to a distributor or wholesaler. They in turn sell to grocery stores themselves. When even a single link in this chain is disrupted, it creates significant ripples throughout the entire supply chain in both directions.
The COVID-19 pandemic disrupted the delicate produce supply chain in ways that grocery stores are still recovering from. Border closures, facility shutdowns, labor shortages and spikes in consumer demand all contributed to difficulties filling supermarket shelves. While some of these pressures were temporary, they revealed deeper weaknesses in the fresh produce supply chain that linger today. As a result of these shifts, grocery stores and supermarkets are still working to reestablish their supply lines and return to pre-pandemic levels.
Climate Change
Planetwide average temperatures are increasing. July 2023 was the hottest month in human history to date. This isn’t a problem of temperatures alone; climate change is bringing extreme weather across the globe. Cold seasons are colder. Rainy seasons are more intense. Storms are more violent.
These combined factors are causing a two-fold problem. First, it’s delaying farmers’ planting timeline, which is disrupting when foods are “in-season” and at their best prices. Second, when crops are planted, extreme weather conditions are leaving them vulnerable to mass dying events and bacterial contamination, resulting in lower yields.
Weather also impacts quality during shipping. Vehicles traveling north and south are more vulnerable to heating from the sun as the broad side of the trailer is exposed to a consistent heat source. As the average daily heat increases, this puts temperature-sensitive products at a greater risk of temperature excursion during transportation.
Increasing Costs
Lower yields combined with rising fuel costs and inflation have contributed to increased difficulties at every step of the produce supply chain. For example, high gas prices have raised shipping rates for growers and distributors who rely on trucking to transport goods. Storage has also become more expensive thanks to wage hikes, the rising cost of real estate, and more.
These price increases eat into profit margins all around, and the costs are passed on to buyers, resulting in fewer sales overall. Growers are shipping fewer products than before and it is simultaneously becoming more expensive for them to do so.
Worker Shortages
Grocery stores have been hit particularly hard with labor shortages along the supply chain, including the ongoing trucker shortage. In fact, 65% of grocery stores noted that they have been impacted by the high employee turnover rates over the last 1-2 years.
Time is of the essence when transporting and storing fresh produce, which has a typical shelf life of only 10-14 days. Staffing difficulties with shippers make it more difficult to move produce already in transit between locations, increasing waiting periods in warehouses and eating into product shelf life.
Quality Control
Pests or pathogens can spread throughout a stock of produce at any stage of the supply chain, from the farm to the grocery store. Pests such as rodents, insects, and birds can enter a warehouse or truck and contaminate the produce. Meanwhile, pathogens such as bacteria, viruses, and fungi can be introduced during harvest or handling if workers have poor hygiene, or if equipment and surfaces are not properly sanitized. Once a single batch of produce has been affected, pests or pathogens can easily spread to other batches through cross-contamination if contaminated and uncontaminated produce are stored in the same bin.
To avoid incidents of foodborne illness, grocery stores must remain vigilant about quality control while produce is in transit. For maximum safety, these efforts should go beyond baseline measures such as regular inspections and the use of proper sealed containers to reduce contaminants’ spread.
For example, maintaining a proper temperature during transportation and storage can prevent the growth of pests and pathogens in fruits and vegetables that require specific temperature ranges. Real-time temperature tracking and monitoring technology can alert suppliers, shippers and grocers of potential issues, allowing them to take corrective action immediately. In addition, pathogen monitoring technology can detect diseases in the stock, enabling fast isolation and removal of infected produce to prevent further waste.
Lack of Supply Chain Visibility
The rise of supply chain visibility technology such as real-time tracking temperature monitors have been a game changer for the grocery industry. Data from these tools enables companies to quickly identify weaknesses in the supply chain, from a warehouse with faulty climate control systems to slow shipping routes. Armed with this information, companies can develop alternative routes, locations or systems to head off quality problems and supply chain disruptions before they start.
Companies that lack this kind of visibility into the produce supply chain suffer a major disadvantage in today’s fast-moving market. By relying on only one insight — whether or not produce is sold — they limit their ability to optimize along their entire supply chain and increase their resilience in the face of ongoing disruption.
3 Solutions to Supply Chain Challenges
Fortunately for grocery stores, technology such as real-time tracking and temperature monitoring can lessen supply chain difficulties such as those listed above. However, technology is only valued if it’s used effectively. Below are a few tips for ensuring grocery stores get the most out of their supply chain technology investments.
1. Backfill Data When Signal Is Lost
Many monitoring and tracking technologies rely on cellular signals to transmit real-time data from sensors distributed in warehouses, vehicles and other locations. When produce is in transit through an area with poor cellular coverage, this can result in data gaps whenever cellular service is lost.
To avoid losing valuable temperature and location tracking data, grocery stores should look for solutions that are able to backfill data gaps. For example, Sensitech’s monitoring technologies continue to store data within the device during service interruptions, so that data can be transmitted as soon as the vehicle enters an area of good cellular signal strength. This ensures grocery stores still have a full set of monitoring and tracking data with no gaps.
2. Leverage a Program Manager for Expertise
Real-time temperature and location monitors generate enormous quantities of data. While most vendors provide dashboards or other portals to organize this information, it can be difficult to know how to act on it.
Best-in-class vendors in the supply chain technology space can offer their expertise to help customers translate information into action. Sensitech assigns each customer a program manager to help interpret their supply chain data, drawing on the company’s 30 years of experience in the space. Program managers flag risky areas, recommend fixes and follow up to track progress over time, yielding continuous improvement on a quarterly review cycle.
3. Use Automation to Alleviate Labor Shortages
As discussed above, staffing shortages are a major stressor for grocery stores at all stages of the supply chain. Automating supply chain processes with technology can mitigate these issues by improving efficiency across company verticals.
For example, when there’s an issue with the condition of a particular shipment of produce, Sensitech devices can send a real-time notification directly to a grocer’s purchasing team, without routing that information through QA. The purchasing team can then immediately begin the process of securing additional stock to replace the shipment in case of rejection.
Final Thoughts
The grocery and supermarket industry plays a critical role in ensuring that fresh, healthy produce is readily available to consumers. However, today’s grocery stores face significant strain on their supply chains, which are still in recovery from the disruptions of the COVID-19 pandemic. Labor shortages, rising costs and quality control issues make it more difficult to get fruits and vegetables from producers’ fields to supermarket shelves.
Sensitech’s range of supply chain visibility solutions alleviates these pressures by enabling grocery stores to monitor and track their products in real time. Armed with Sensitech’s suite of monitoring devices, cloud-based software applications and analytics tools, grocers gain insight into the strengths and weaknesses of their supply chains so they can resolve issues before they cause major disruptions. By ensuring products are kept at the right temperature and conditions throughout the supply chain, Sensitech's cold chain solutions also reduce waste and improve product quality.
If you’d like to learn more about how Sensitech can help grocery stores avoid spoilage and contamination, boost shipping efficiency and more, Contact Us today.