How EU GDP Guidelines Impact Cold Chain for Pharmaceutical Products
Identifying the Challenges that Influence Safety and Quality
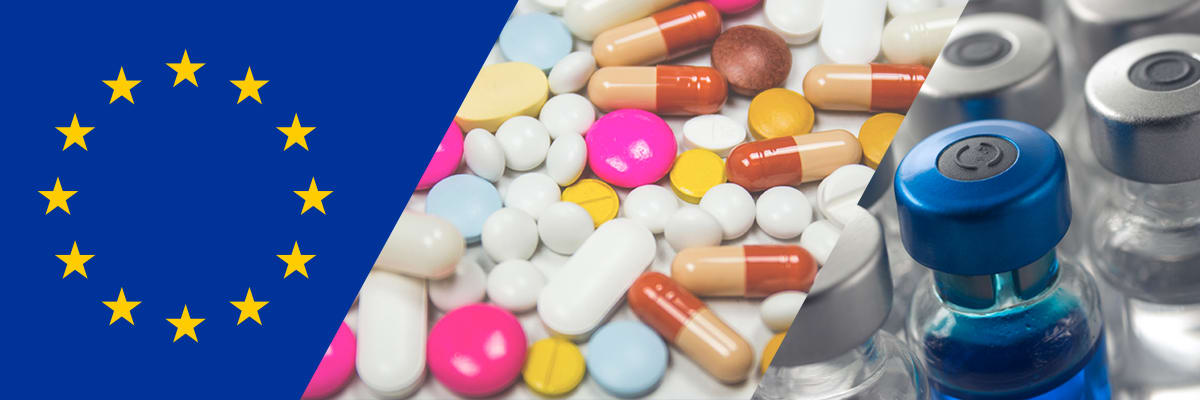
The European Guidelines on good manufacturing and distribution practices are designed to propose a framework for regulations to ensure the safety and quality of pharmaceutical products and ultimately the safety of the consumer and patient.
The basis of the EU GDP Guidelines is that storage areas and facilities must be controlled. This includes temperature, humidity, lighting, cleanliness, etc. where applicable, in order to control as many aspects as possible that can influence the safety and quality of a pharmaceutical product.
The Sensitech Life Sciences Professional Services team works with customers to identify challenges and primarily focuses on two key factors that influence safety and quality: temperature and humidity. Depending on the local climate and the stored product, the focus can be on temperature only, or both temperature and humidity. In Europe, the main focus is on temperature. We assist clients with the implementation of the GDP Guidelines by performing multiple projects. An example of such a project is a temperature mapping exercise, something that has been highlighted specifically in the EU GDP Guidelines:
- An initial temperature mapping exercise should be carried out on the storage area before use, under representative conditions… The mapping exercise should be repeated according to the results of a risk assessment exercise or whenever significant modifications are made to the facility or the temperature controlling equipment… (EU GDP/GMP; Commission guideline 2013/C 343/01, Chapter 3.2.1)
At Sensitech®, we advise our customers to perform at least three temperature mapping exercises: one before the storage area will be used (empty mapping) and two seasonal (summer and winter) mappings once the facility is in use to identify any issues with the temperature management during the most extreme weather circumstances. Our team defines "storage area" as “every area in a facility where temperature sensitive product is held for extended periods.” The team focuses not only on the designated storage area but also quarantine, quality, inbound/outbound, and any other areas where product is being handled. Each of these areas will be mapped. Combined with information from the site-visit and additional temperature information from heating, ventilating and air conditioning (HVAC) systems and exterior temperatures, a thermal mapping results in a clear overview of the facilities performance regarding temperature management.
It is important to keep in mind that each time the facility is updated, whether it is a change to the HVAC settings, the extension (or decrease) of a storage area’s size, or an adjustment to product storage heights, etc., the mapping results could be invalid. The Quality team at the facility should be mindful of changes and their possible impact, and should assess if a remapping is necessary. In general, Sensitech’s Professional Services will advise a customer to remap if any invasive changes are being made, such as the replacement of a HVAC unit, reconstruction of the (storage) area, or after five years. The bottom line is that each action should be assessed in order to ensure product quality and safety at all times.
Want to learn more? Contact us here.