Next Steps After Identifying Cold Chain Issues
How to Fix Problems in Your Temperature-Controlled Supply Chain
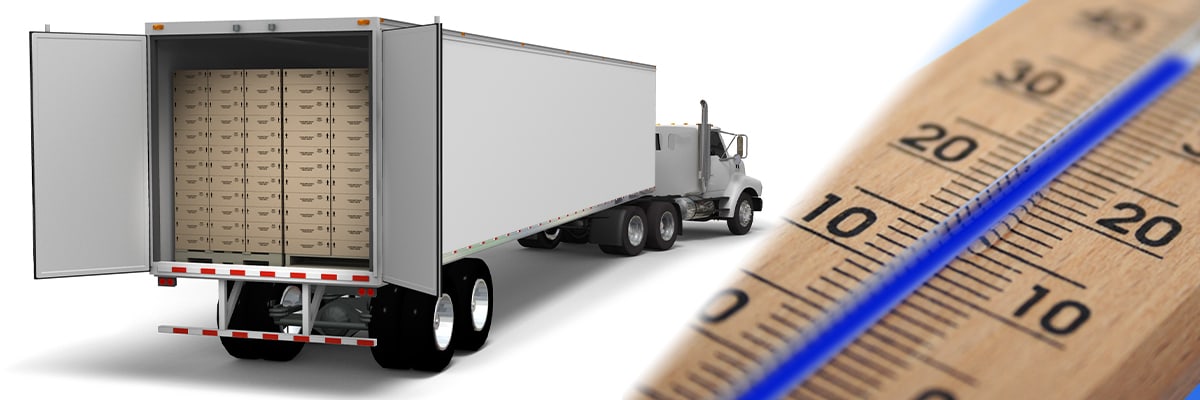
Modern cold chain management is a process of continual improvements and fine-tuned optimizations. Technological advances – such as real-time temperature monitoring and thermal mapping – are identifying cold chain issues as they occur and enabling organizations to take action while their products are still in transit.
But how exactly can an organization intervene when they detect temperature excursions and other cold chain issues on a shipment in progress? That’s where Sensitech comes in.
What Happens When a Cold Chain Fails?
When it comes to food, even slight temperature excursions can have an impact on the overall product quality. However, temperature abuse (meaning when the product is not stored at the correct temperature) can cause food safety concerns requiring a recall of an entire shipment.
Even more dangerous are cold chain issues affecting medicines, like vaccines. Temperature-controlled medication storage has almost no margin for error. Even a brief temperature excursion can cause a batch of vaccines to become ineffective, potentially endangering anyone who received a dose and believed they were inoculated.
For these reasons, organizations should utilize real-time temperature monitoring and take action as soon as they identify a cold chain issue.
Five Steps to Resolving Cold Chain Issues
Contrary to popular belief, temperature problems in a refrigerated trailer are rarely caused by malfunctioning equipment. Rather, they are almost always the result of a process issue.
The following five steps explore our recommended process for identifying the root cause of a cold chain issue. Follow these steps and do your best to answer these questions:
Step One: Document how the refrigeration unit was programmed
- What temperature set point was used?
- Is there evidence suggesting the temperature set point or the reefer mode was changed, or that the unit was shut off during transit?
- What refrigeration mode was used - Continuous or Fuel Saver mode?
- Continuous mode keeps the refrigeration compressor running and makes minute adjustments, resulting in that result in very consistent temperatures. Fresh perishables should utilize continuous mode.
- Fuel Saver mode allows the temperature to fluctuate.
- What defrost setting was used?
Step Two: Obtain documentation of the loading temperature
If possible, obtain the shipper’s records for product temperature at the time of loading.
If the shipper cannot provide loading temperature records, it is an indication that care may not have been taken to ensure loading occurred at the proper temperature. If the center of the pallet is warm, and the outside is colder, this is often an indication that the product was loaded warm.
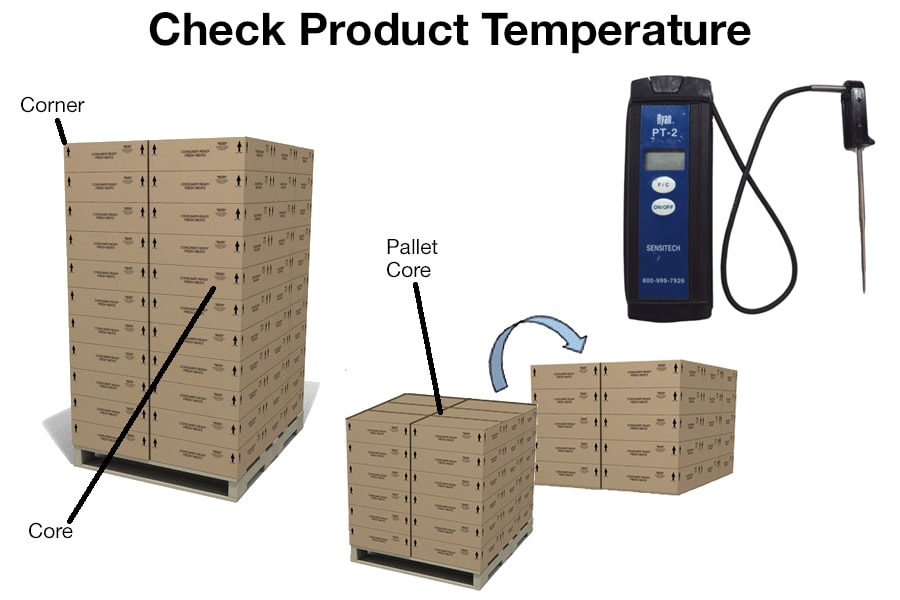
Step Three: Document how the product was loaded on the trailer
Proper loading is important to ensure good airflow throughout the trailer.
- Is the load stacked above the red line?
- If the trailer has no red line, is the top of the load impeding airflow or constricting the air chute?
- Are the pallets touching the walls and doors of the trailer?
- This is common for shipments in Europe, as the dimensions of the trailers and pallets leave little free space. Ideally, there should be at least a small gap between the pallets and the wall to allow airflow and prevent the product from conducting heat through the wall.
- What defrost setting was used?
Step Four: Document the condition of the trailer
- Is the air chute damaged?
- A damaged air chute can cause the airflow to short circuit, meaning most of the air supply gets diverted to the refrigeration-unit end of the trailer, and does not reach the door end of the trailer. The resulting poor air flow often results in high temperature recordings at the door end, often showing a day/night cycle, with good temperature recordings at the end of the trailer near the refrigeration unit. This pattern is also common when the product is loaded too high or when the return air vent is blocked.
- Is there damage to the walls, ceiling, floors or doors?
- Are there any gaps caused by damage to the door seals?
- Are kazoos in place on the drains?
- Kazoos are the rubber devices on the outside of the floor drain tubes which allow water out, but block air.
Step Five: Document any evidence that the doors were opened during the trip
- Does the TempTale temperature graph show a sharp spike in temperature during transit? (not to be confused with defrost spikes)
- If using a TempTale Geo, are there light sensor readings during transit?
- Did the trailer stop to load additional product along the way?
- Did the trailer arrive without the seal or with a broken seal?
Resolve Your Cold Chain Issues with Sensitech
At Sensitech, we have a team of experts specializing in refrigeration, food science, life science, logistics, and process improvement. Our professional services and project teams provide services and support to our customers to help them continually improve their cold chains. If your temperature monitors have identified a cold chain issue you can’t explain, our team is here to help.
For more information, contact one of our Sensitech experts today.