Understanding Cold Chain Regulations for Animal Health
Good Cold Chain Management Practices (GCCMP) — Are Your Veterinary Pharmaceutical Products Compliant?
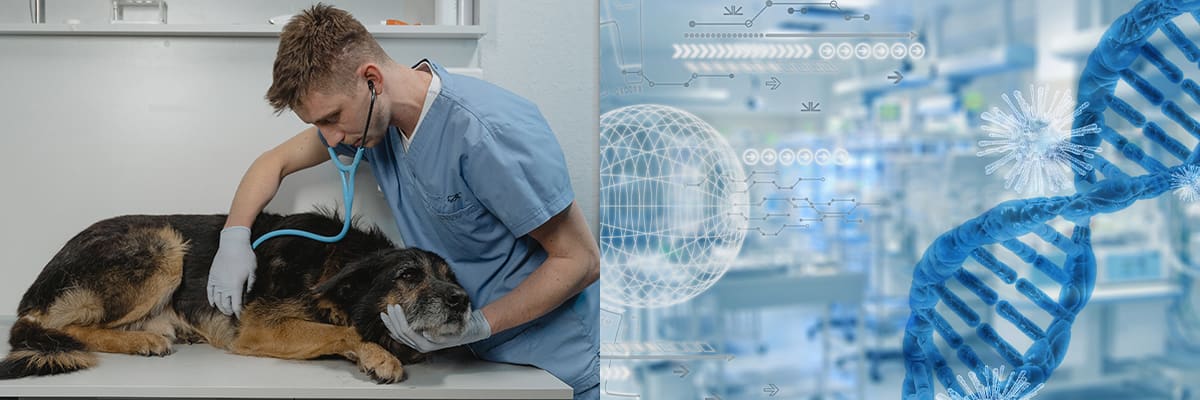
Animal health products, including vaccines, medicines, and medical devices, are subject to regulations that seek to ensure product quality, effectiveness, and safety.
Recent regulatory guidelines in the EU have harmonized GCCMP for veterinary products, outlining practices for their proper transportation and storage. European regulations for the distribution of veterinary medicinal products are now in line with those for pharmaceutical products designed for human use, placing increased scrutiny on temperature monitoring to ensure product quality and safety.
This is not only a European concern: In the United States, veterinary products are already subject to similar regulations and the UK has developed its own guidelines based on the EU regulations. Understanding how to comply with these regulations is critical.
Veterinary Medicinal Distribution Guidelines Defined
Regulation (EU) 2021/1248, effective from August 2021, outlines Good Distribution Practices (GDP) for veterinary medicinal products in accordance with Regulation (EU) 2019/6 of the European Parliament. These standards seek to harmonize animal health regulations across the EU, bringing distribution expectations for veterinary pharmaceuticals in line with those for products designed for human use.
Key requirements of these regulations include:
- Risk assessments
- Demonstration of temperature control during transportation and storage
- Detailed documentation in a quality management system
- Calibrated and qualified or validated equipment
- Temperature monitoring
This regulatory framework applies to products entering, exiting, or moving within Europe at any point in their distribution. Manufacturers, 3PLs, and wholesalers need to be aware of and comply with these regulations.
While no longer part of the EU, the United Kingdom’s guidance has the EU regulations as their foundation and distributing and storing animal health products in the UK has near-identical temperature control requirements.
In the United States, veterinary products fall under USP <1079>. As in the EU, regulations for veterinary and human use products are harmonized, including quality management, GDP, temperature monitoring, and temperature mapping.
Note that in the U.S. veterinary drugs and vaccines do not fall under the same regulatory bodies, adding a complication for distributing and storing animal health products. Drugs fall under the Veterinary division of the FDA while vaccines and biologics are regulated by the U.S. Department of Agriculture.
In-Transit Monitoring Technology Considerations
During transit, temperature monitoring is essential to assure the quality and safety of veterinary medicinal products. Two types of temperature monitor most effectively meet this need: indicator and datalogger monitors.
An electronic temperature indicator gives a visual indication of whether a shipment remained within its ideal conditions, with multiple configurable alarm settings to meet a product’s specific transport requirements. Indicators are simple, compact, and inexpensive, while being accurately calibrated to NIST® standards for regulatory purposes.
If the goal is to support an audit, assess risk, or make improvements to the distribution process, a datalogger is the way to go. A datalogger provides much more detailed data than an indicator, recording time-stamped temperatures at frequent, configurable increments. This data can be stored in the cloud, saved in an encrypted file to be used with desktop software for post-shipment analysis and record keeping, or shared as a secure PDF. Dataloggers should be fully validated with multiple alarm limits.
In order to meet compliance requirements, temperature monitors must be validated with validation artifacts demonstrating that the devices have passed rigorous accuracy testing.
The primary objective of temperature monitoring is to demonstrate temperature control during the product’s journey. Additional benefits include utilizing temperature monitors to improve supply chain logistics, which makes regulatory compliance easier, saves money in product loss, and even enables moving to lower cost distribution methods once risk has been accurately assessed.
Storage Monitoring Considerations
When selecting and implementing a facility monitoring system, the goals should be centered on four objectives:
- Regulatory compliance
- Assuring temperature control
- Increased visibility
- Achieving higher operational efficiency
Businesses must do their homework before selecting a 21 CFR Part 11- and EU GMP Annex 11- compliant system. They must ensure that the provider can provide a comprehensive qualification package in which all critical events—alarms, alerts, system logins, corrective and preventative actions—are easily identifiable and traceable to the person who carried them out. A regulatory compliant system will generate data to support an audit trail for all system activities, with secure and regulated access to various levels of information and actions.
To ensure that the system will adhere to the required design criteria, has been installed appropriately, runs as intended, and meets user requirements, the qualification package should include installation with operational and performance qualification. Furthermore, the monitoring apparatus itself should be calibrated annually and replaced as necessary.
By automating data collecting and providing easy access to the data from anywhere via a secure web browser, a facility and/or equipment monitoring system can help businesses improve operational efficiency. The chosen solution should be simple to deploy and scalable as storage needs change over time.
Thermal Mapping Guidance
Facilities and equipment used to store veterinary pharmaceuticals should be thermally mapped according to global regulatory and standards-based recommendations for the products’ storage, handling, and distribution. This assumes that the company's quality management system will have the necessary documentation to prove that a state of control can be maintained within storage locations and that the justification for the locations of temperature sensors is sound.
Because of this, it is strongly advised that a thermal mapping be conducted before installing a stationary monitoring system. This thermal mapping will also serve as a scientific record of the methodology utilized in the monitoring system. Without a comprehensive thermal mapping, there is little or no evidence to support the monitor placement protocol, putting the business at regulatory risk. Learn how thermal mapping works in practice.
Conclusion
The importance of effective temperature management techniques for animal health products is being emphasized and enforced by regulatory organizations around the world. Temperature monitoring, risk assessments, thermal mapping, and recorded evidence of adherence to environmental parameters are required whether an animal health product is in-transit or in storage. Implementing best-in-class temperature monitoring technologies at every step in the journey can reduce risk, help ensure compliance, and provide the data required to drive operational improvements, protecting product quality and safety while optimizing cold chain efficiency.
For more information about veterinary pharmaceutical product compliance, Contact Us today.