11 Steps to a Successful Warehouse Temperature Mapping Study
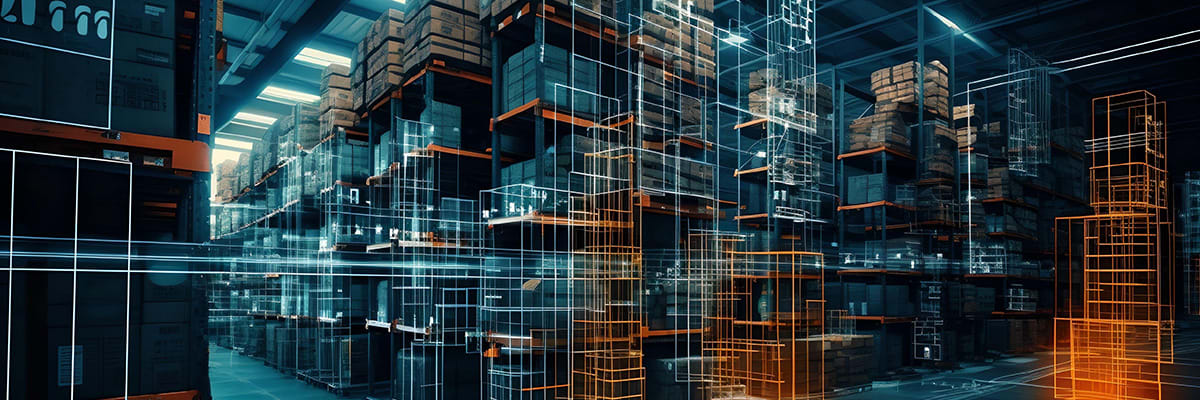
What Is Warehouse Temperature Mapping?
Warehouse thermal mapping is the process of identifying risk areas for temperature-sensitive products in a storage facility. It plays a crucial role in maintaining product quality and regulatory compliance within the cold chain. The goal is to measure thermal conditions inside a facility’s cold rooms and freezers to evaluate performance under normal operating conditions.
By monitoring temperature variations over time and across different locations, a study can flag potential issues before they do any damage to sensitive products like food and medicine. That can protect your product and keep you compliant with government regulations. But how exactly is a temperature mapping study conducted and what can your organization do to get the most accurate results? The Sensitech professional services team is here to guide you through each step of the process.
How Is Temperature Mapping Done?
In a temperature mapping study, temperature monitoring devices are strategically placed throughout the warehouse to precisely record temperature variations over time. Arranging sensors in a grid pattern with both horizontal and vertical layers helps maximize coverage, but every space is different.
It’s best to work with an expert to determine an optimal arrangement of temperature monitors for your specific warehouse. Make sure to take into account potential sources of thermal fluctuations like windows and doors. Large organizations with multiple warehouses should develop consistent, streamlined mapping protocols they can apply across all facilities.
A temperature mapping study typically occurs over a two-week time period to capture variations between different times of day and days of the week. It’s a best practice to map each warehouse when it’s empty and again when it’s fully loaded with inventory to determine whether product storage has an impact on results. An organization may also repeat the mapping at different times of the year to capture seasonal changes in temperature.
By gathering temperature data in precise detail, a thermal mapping study helps an organization identify the specific location and timing of unwanted temperature excursions. Once they’ve pinpointed these issues, organizations can take corrective measures to solve them, safeguarding product quality and regulatory compliance.
What Should Be Tested During a Warehouse Temperature Mapping Study?
A thorough temperature mapping study should collect data in many different conditions to create a complete picture of the warehouse’s thermal environment. The following aspects are typically tested in a temperature study:
Normal Conditions
Part of the study includes temperature monitoring during normal operations, covering two full work days and two full weekends. This accounts for temperature variations based on different days of the week.
Seasonality Test
Different seasons are considered to evaluate temperature fluctuations throughout the year, particularly fluctuations that occur between winter and summer.
Empty Warehouse Test & Loaded Warehouse Test
Temperature mapping is conducted for both empty and fully loaded warehouses to assess the impact of product storage on temperature distribution. This step may be skipped if the warehouse is already established and full of product.
Humidity
In addition to temperature, humidity levels are also monitored during the mapping study to ensure optimal storage conditions for temperature-sensitive products.
Additional Customer Tests
Depending on specific requirements, customers may request additional tests such as generator recovery tests.
Why Warehouse Temperature Mapping Matters
If your organization stores any temperature-sensitive products, warehouse temperature mapping isn’t just nice to have, It’s a must. Here are a few reasons why:
Ensuring Effectiveness of Medication or Product
With temperature-sensitive products such as food or medicine, a change of even a few degrees can damage or spoil the product. By mapping the temperature conditions, you can ensure that the storage areas maintain the required temperatures to preserve product integrity.
Proving and Verifying Temperature Compliance
Temperature mapping enables you to validate that storage areas consistently maintain the required temperatures. This verification is crucial for regulatory compliance and provides assurance to customers and stakeholders.
Mitigating Fluctuations in Temperature
Temperature fluctuations within a warehouse can occur due to various factors such as layout, air circulation, and outdoor weather conditions. By identifying these fluctuations through mapping, your organization can take proactive measures to mitigate temperature variations and maintain product quality.
Identifying Risk Areas
Warehouses are complex environments with many factors contributing to temperature variations. For example, a product stored directly under a vent or a light will not be the same temperature as a product stored at ground level. Temperature mapping identifies high-risk areas such as locations near doors, windows, or areas with less HVAC equipment. By pinpointing these risk areas, you can implement targeted solutions to ensure a consistent, controlled temperature inside the warehouse.
Why Warehouse Temperature Mapping Matters
If your organization stores any temperature-sensitive products, warehouse temperature mapping isn’t just nice to have, It’s a must. Here are a few reasons why:
Ensuring Effectiveness of Medication or Product
With temperature-sensitive products such as food or medicine, a change of even a few degrees can damage or spoil the product. By mapping the temperature conditions, you can ensure that the storage areas maintain the required temperatures to preserve product integrity.
Proving and Verifying Temperature Compliance
Temperature mapping enables you to validate that storage areas consistently maintain the required temperatures. This verification is crucial for regulatory compliance and provides assurance to customers and stakeholders.
Mitigating Fluctuations in Temperature
Temperature fluctuations within a warehouse can occur due to various factors such as layout, air circulation, and outdoor weather conditions. By identifying these fluctuations through mapping, your organization can take proactive measures to mitigate temperature variations and maintain product quality.
Identifying Risk Areas
Warehouses are complex environments with many factors contributing to temperature variations. For example, a product stored directly under a vent or a light will not be the same temperature as a product stored at ground level. Temperature mapping identifies high-risk areas such as locations near doors, windows, or areas with less HVAC equipment. By pinpointing these risk areas, you can implement targeted solutions to ensure a consistent, controlled temperature inside the warehouse.
Setting Up a Warehouse Temperature Mapping Study
To ensure your warehouse temperature mapping study delivers accurate, actionable results, follow these key steps:
1. Create a Plan
To start, define the objective of the temperature mapping study. For example, if the warehouse is a new facility, the objective may be to prove that it’s ready to launch.
From there, develop documentation and procedures accordingly. Start by gathering specifications and requirements for the products being stored in each area of the warehouse. This lets you define the acceptable temperature range in each area, such as cold rooms and freezers. Finally, establish controls to ensure accurate and reliable data collection.
2. Identify Areas of Risk
Locate specific factors within the warehouse that could cause temperature fluctuations, such as docking areas, floor storage areas near dock doors, AC units, windows, and areas with less HVAC equipment. By identifying these risk areas at the outset, your organization can focus monitoring efforts accordingly.
3. Set Protocols
Determine the study duration, parameters for acceptable temperature fluctuations, and guidelines for acceptable excursions. For example, certain products may be able to tolerate temperatures out of the normal range for up to 24 hours, making that an acceptable excursion.
4. Distribute Sensors
Map out the sensor layout in a 3D space, placing sensors approximately 30 meters apart in a grid pattern. Placing sensors both vertically and horizontally will allow you to pinpoint areas of concern and identify hot and cold pockets throughout the facility. Additional sensors should be placed at high-risk areas, taking into account air flow across the space. When in doubt, err on the side of using more devices to maximize coverage across the full study area.
5. Select Sensors
Choose precision stationary temperature monitors with long-term stability to ensure accurate and reliable temperature monitoring throughout the study. Sensitech’s flexible, wireless sensor networks collect and transmit data in real time, allowing for easy monitoring of progress.
6. Set up Sensors
Install and configure the temperature monitoring sensors according to the established plan. Ensure that the sensors are functional and accurately reporting temperature data.
7. Review the Data
After the designated time period, review the collected data. Analyze the data using graphs and other visual representations to identify high-risk zones and areas with temperature deviations.
8. Identify Pain Points
With your study results in hand, begin to look for potential explanations for any excursions. Air flow issues are a common culprit, so make sure to check the positioning of HVAC units against your thermal map. Warehouse tools may also be heat contributors. For example, forklift exhaust can raise temperature noticeably in some cases.
9. Take Corrective Actions
Once you identify what’s causing temperature fluctuations, you can take corrective actions. For example, adding curtains in transition areas — such as between cold rooms — can reduce unwanted air flow. Alternatively, teams may add fans to improve air flow throughout the facility. Some fluctuations may also be the result of human error, such as employees not following proper door opening protocols. In these cases, additional training or updates to standard operating procedures may be necessary.
10. Create Report
Finally, you should prepare a comprehensive report summarizing the findings of the temperature mapping study. Sensitech's reports provide detailed information identifying areas of concern, potential corrective actions, and recommendations for permanent sensor placement.
11. Conduct Another Study Down the Line
It is advisable to conduct periodic temperature mapping studies (typically every 3-5 years) to ensure ongoing compliance and identify any changes or issues that may arise over time. This helps maintain a robust temperature control system and provides a record of continued adherence to regulatory standards.
Case Study: Finding a Solution With Warehouse Temperature Mapping
In the life sciences industry, proper storage of temperature-sensitive medicines is critical to maintaining their efficacy. A large pharmaceutical company came to Sensitech to conduct a thermal mapping study of their facilities with the goal of improving temperature management and regulatory compliance.
Sensitech’s two-week-long study identified a procedural issue where the cold room's door was left ajar during work, leading to hot air entering the cold room and cold air circulating into the warehouse storage area. Patterns in the data indicated simultaneous hot and cold excursions occurring in close proximity, caused by improper door management and an incorrect set point temperature.
Based on this analysis, Sensitech recommended specific actions to improve temperature management in the customer’s warehouse and cold room. New standard operating procedures were implemented to prevent excursions caused by door openings. The study also prompted the replacement of damaged insulation, resulting in cost savings and mitigation of high-temperature excursions. At the conclusion of the project, Sensitech provided audit-ready documentation of improved temperature controls, demonstrating regulatory compliance across the customer’s storage environment.
Choosing the Right Monitor for a Warehouse Temperature Mapping Study
Selecting an accurate and reliable temperature monitoring device is crucial for a successful temperature mapping study. The quality of the data you collect has a direct impact on your ability to diagnose problems and determine effective next steps. Sensitech offers real-time temperature monitoring systems that provide live updates of the data, allowing your organization to identify temperature fluctuations as they occur. This immediate access to data enables timely action and investigation into the causes of temperature variations.
Unlike traditional monitoring devices that require manual retrieval and downloading of data, Sensitech's systems provide continuous and automated data collection, ensuring accurate and up-to-date temperature information. This feature empowers organizations to make informed decisions based on real-time data, enhancing their ability to maintain product quality and regulatory compliance.
Final Thoughts: Your Next Warehouse Temperature Mapping Study
Warehouse temperature mapping is a critical process for ensuring the integrity of temperature-sensitive products and compliance with regulations. By conducting thorough temperature mapping studies, organizations can identify risk areas, mitigate temperature fluctuations, and take proactive measures to maintain product quality throughout the supply chain.
With 20 years of experience in thermal mapping, Sensitech is a reliable partner for organizations seeking to optimize their temperature control processes. Every Sensitech temperature mapping project follows a thorough, stress-tested process.
A dedicated project manager customizes the mapping protocol for each client. Customers who opt to place their own sensors receive detailed self-execution training to ensure accurate results. This ensures that all sensors are properly calibrated to capture data at a level of detail competitors often fail to match. After each study, Sensitech also provides high-quality, audit-friendly documentation showing proof of customers’ compliance with regulatory standards.
To learn more about how Sensitech can help with your next warehouse temperature mapping study, Contact Us today.